March 21, 2021
Check mark number 3: Lithium Iron Phosphate Batteries installed!
-
New Galley CounterInstall an Air Conditioner- Repair Dry Rot in Head Bulkhead
Install Lithium Batteries- Replace Transmission Damper Plate
We can leave it at that, unless you’re technically minded (or a glutton for punishment). If you are, read on.
We had four Trojan T105 lead-acid batteries for a 450 amp-hour battery bank. We installed air conditioning to get ready for the heat of Indonesia and with that install, we had two goals for batteries: offset the weight of the air conditioner addition and get enough power to run the aircon for at least an hour a day. To achieve these goals, we decided to make the move to lithium batteries.
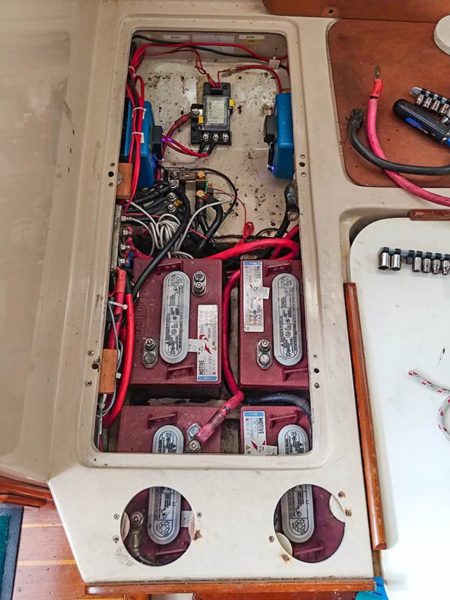
Here’s the weight savings we’ve realized…
We’re 58 Kg (or 128 lbs) lighter with the lithium batteries. The air conditioner weighs about 18 Kg (40 lbs.) including the water circulating pump, so net, we’re 40 Kg (88 lbs.) lighter. Bring on the ice cream!!!
Power Calculation:
With our 450 Ah or lead-acid batteries, we could charge them daily to 90% and use them down to 50%. To charge lead-acid batteries to 100% takes a long time – usually not practical. To preserve battery life – you don’t really want to discharge below that level. These numbers make our usable capacity 180 Ah.
Lithium batteries can be charged to 100% as they take almost full charge current right up until they get full. They can be discharged almost completely, but let’s call 10% safe. That’s 90% usable capacity of our new 400 Ah battery bank capacity for 360 Ah total usable power.
With the new batteries, we doubled our available battery power!
What Batteries?
We bought battery cells and BMS units (Battery Management Systems) from AliExpress (I was going to assemble them myself) and waited almost two months before they told us they couldn’t ship them to us in New Zealand. I scrambled around and found someone here in Auckland that imports similar batteries already assembled and in a stainless steel case for not much more money. Here’s what they look like:
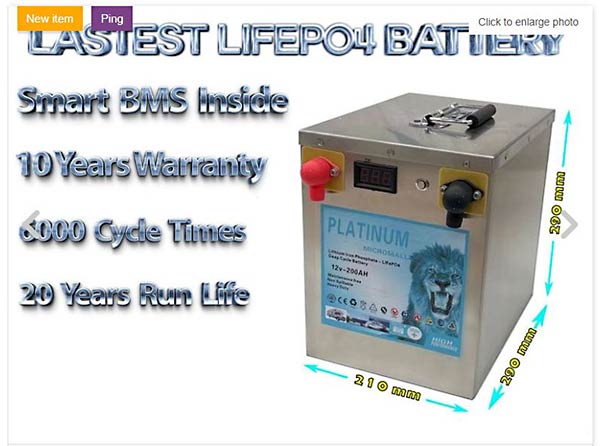
Are they good quality? I opened up the case and inspected the batteries. The workmanship looks excellent. All lithium batteries of this type are made up of individual 3.4 volt cells. All these cells are made in China at one of just a few factories. Basically, the battery cells are pretty much all the same. If you aren’t assembling your own battery from cells, the difference is the workmanship. I’m very happy with what I see in these batteries. Time will tell the whole story.
Are they safe? Lithium batteries are made from several different chemistries. The ones that get the bad rap are not lithium iron phosphate (LiFePO4) like our new batteries. These might be safer than lead-acid batteries. Here’s a video that shows just how safe they are. Keep in mind that they are destroying several types of lithium batteries. Ours are LiFePO4 (or LFP).
And speaking of destroying, here’s what our boat’s looked like for the past week…
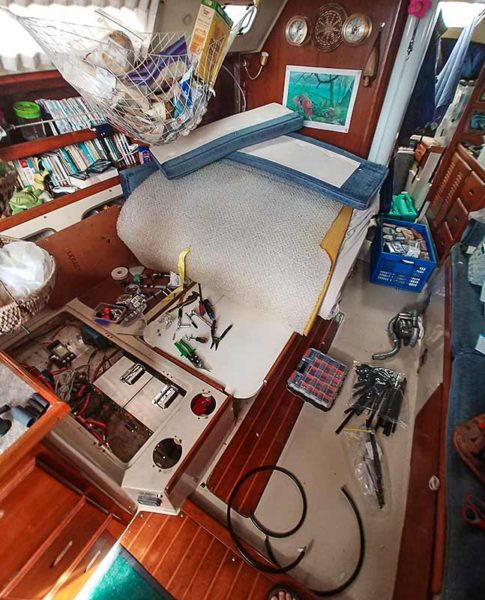
And here are a few pictures of the completed installation:
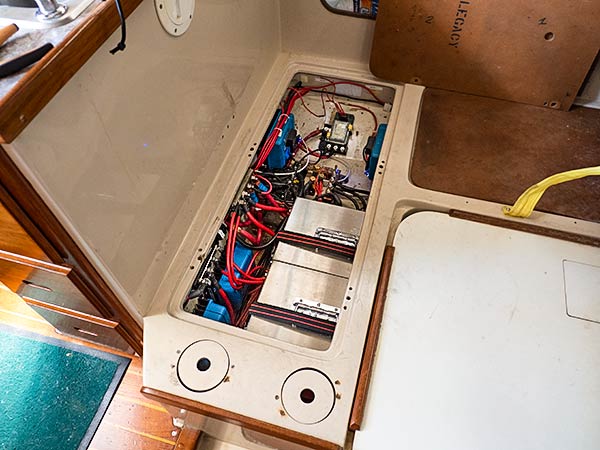
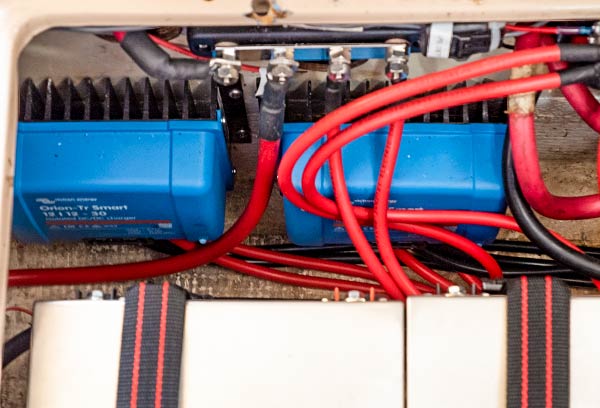
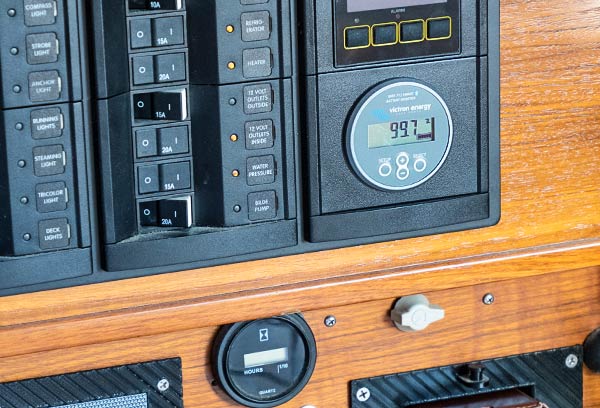
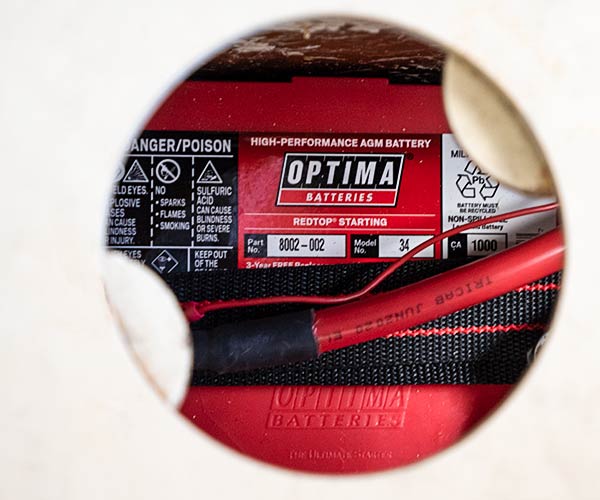
Here’s our system diagram.
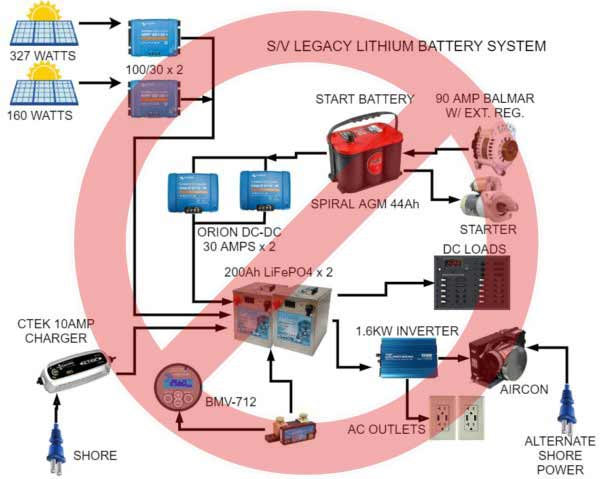
An issue with lithium battery installations on a boat is that the battery can be unexpectedly disconnected from the system by its internal BMS (Battery Management System). If this happens while the alternator is putting out a lot of power, it can destroy the alternator or worse yet, a voltage spike can destroy all the electronics on the boat.
To prevent this, there are several complicated schemes, none of which interested me. I instead chose to install a separate start batter (we’ve never had one before) and charge that small battery with the engine alternator. While that’s charging, two 30 amp, Victron Orion-TR DC-DC converters charge the lithium house bank. We use two of these to get 60 amps of charge current.
This also limits the power coming from the alternator. Because lithium batteries can take about all the power you can throw at them, the alternator can be damaged from overloading and overheating. This DC-DC scheme solves that issue as well.
The start battery we chose is an Optima spiral-wound AGM battery. It’s only 44Ah, but according to Optima, there is no limit on charge current (as long at the battery stays below 125C).
OK, that’s all I’ve got and the culmination of two years of research. We’ll see if it all works. Cross your fingers! -Rich
Update: May 21, 2021
We’re out for a little shakedown cruise and the batteries are incredible, with one exception: the DC to DC converters are getting too hot (the cases get to 150° F, 65C). I knew this was an issue before we left and ordered fans for them, but instead, during a brief stop at a marina, I made a change in the system.
I rewired the system so that the alternator is now charging the lithium house bank. I am using one Victron Orion TR DC to DC converter to change the starting battery form the house bank.
The reason I didn’t do it this way from the start was to protect the alternator and boat electronic systems from a voltage spike caused if the battery management systems took the lithium batteries off line. Now, to protect the system, I installed a Sterling Alternator Protection Device (APD) across the alternator. Also, I hope is that the load of the DC to DC converter would also help protect the system in the case of a battery disconnect.
I replaced a faulty Balmar alternator temperature sensor and have the alternator regulator set to limit the alternator to 100 C. I also set the belt manager to #1 to de-rate the alternator output a bit.
As it sits now, I’m getting about 60 amps from our 90 amp alternator. It gets hot enough to throttle back about every fifteen minutes with the output droping to around 20 amps for two minutes.
The DC to DC converter, now charging the start battery, stays cool as it doesn’t have much work to do to keep the starting battery charged.
Here’s our revised system drawing…
During our May NZ cruise, I got a good chance to see the new system working and I’m thrilled. The only issue we had was that the battery monitor wasn’t tracking the SOC (state of charge) well. I could tell this because when we were motoring (and charging), the battery voltage would reach 14 volts (the point I’d set for maximum), the charging current would drop to close to zero and the monitor would read about 85% SOC.
I was lowering the charge efficiency factor 2% at a time to try to correct this. I got down to 89% and it was getting closer but it was not perfect. Changing the Peukert’s exponent from the recommended 1.05 to 1.00 fixed this and I was able to bring the charge efficiency factor back to 95%. Now the tracking is very close to perfect.
Update: April 12, 2022
It’s been just over a year with our lithium batteries, and though Covid has prevented offshore cruising, we have used them quite a bit. At the berth, we seldom plug in the AC, relying on batteries and solar instead.
An article from Marine How To was sent on the Pacific Puddle Jump email list. It was a great read with lots of food for thought and I’ll link it here. I’m not in 100% agreement with him, but he makes a lot of great points. It’s prompted me to plan a 1-year-checkup on my batteries.
The one thing I don’t mesh with is the requirement for the battery BMS to send a signal before disconnecting the battery from the system. Yes, that would be great. No, it’s not going to happen with current state of what’s available on the market.
ABYC says: If a shutdown condition is approaching, a BMS should notify the operator with a visual and/or audible alarm prior to disconnecting the battery from the DC system.
Only a couple of very expensive batteries have such a signal wire that can be used to stop alternator charging (field control) or sound an alarm. It seems that this requirement has been interpreted to allow for a Bluetooth display of BMS status on a phone. I argue that in real life, no one will ever see such a display in time to stop the alternator.
It did make me wonder about the condition of my lithium batteries and if the cells were staying balanced. When I installed my batteries, I bought two BMS units with Bluetooth, but when I couldn’t get the bare cells shipped form China, I went with batteries that had an integrated BMS with no communications. I thought I’d open my batteries and check the cell balance level manually. If they were out of balance, I’d install the Bluetooth BMS units instead of their built-in BMS. It would be nice to be able to check cell balance periodically without disassembling the battery cases, but if it ain’t broke, I ain’t goin’ to fix it.
Cell Voltages:
Starboard Battery
cell 1 – 3.345 volts
cell 2 – 3.345 volts
cell 3 – 3.345 volts
cell 4 – 3.345 volts
Port Battery
cell 1 – 3.339 volts
cell 2 – 3.340 volts
cell 3 – 3.339 volts
cell 4 – 3.339 volts
There’s nothing to fix there. Only 1 mV difference and only in one cell. The reason the port battery voltages were lower is that I took out and tested the starboard battery first while the port battery continued to discharge.
Another maybe minor issue is that on the little cruise we’re on now, I found that the battery monitor was very much overestimating the battery state of charge. When the monitor got to 100%, the batteries were still at about 13.5 volts and taking 50 amps. Definitely not at 100%.
I had the Victron BMV-712 monitor charge efficiency set to 95% as per recommendations I found online. But when I look at the statistics on the battery monitor history, I find this… Discharged energy 220.6 KWh, Charged energy 256.4 KWh. Doing the division says that only 86% of what’s gone into the batteries has come out. That’s 86% efficiency. Lithium should be more efficient than that, but that’s what I’ll set it to now and see how it works out.
It’s possible that the cause of this lower than expected efficiency is that the cell balancing on the BMS seems to be resistive. It’s usually done with FETs that dissipate a lot less power as heat. Here’s a picture of the BMS…
Issue 3… There was quite a bit of rust on the stainless steel battery cases. The picture below shows the crevice corrosion after cleaning it up with Barkeepers Friend.
After cleaning, I treated it with a corrosion inhibitor spray. I hope that’s enough.
Update: January 25, 2024 (almost 3 years after install)
Cell Voltages:
Starboard Battery
cell 1 – 3.287 volts
cell 2 – 3.286 volts
cell 3 – 3.286 volts
cell 4 – 3.285volts
Port Battery
cell 1 – 3.279 volts
cell 2 – 3.281 volts
cell 3 – 3.280 volts
cell 4 – 3.280 volts
The difference between cells was only 0.002 volts. This was with the batteries at about 25% SOC and it had been about three weeks since they’d been up to 100% SOC. The difference between port and starboard batteries was because I test one battery while the other is in use, then swap them to test the other battery.
I was considering some changes to the settings on the Balmar regulator. I decided to leave well enough alone. Here’s more about that.
Just a note about the system to date:
The Balmar high output alternator failed in New Caledonia. I had it repaired in New Cal and it wasn’t that big a deal to get it fixed. I decided to get rid of the unreliable and troublesome Balmar alternator while we were in Australia. We installed a Bosch alternator and it’s great. There’s more about that here.
The 10 amp battery charger in the diagram failed and I replaced that with a 15 amp Victron charger. Some people say that these small chargers aren’t big enough for our 400 amp-hour battery bank, but I’m not trying to fully recharge the bank overnight. When we have access to shore power, it’s often for days or weeks while we’re at a dock. The 10 amps was plenty (with our solar as well). The 15 amps has been more than enough.
Here in Indonesia we’re having a very hard time finding propane or lpg. We bought an electric kettle for coffee making to save gas and now, a little drip coffee maker (more here). We also treated ourselves to a toaster. Wow, the luxury. The electrical system is handling the larger demands just fine and we’re now getting about 6 months from a 7kg cooking gas tank (which we have to fill by gravity transfer from a local gas cylinder).