November 11, 2018
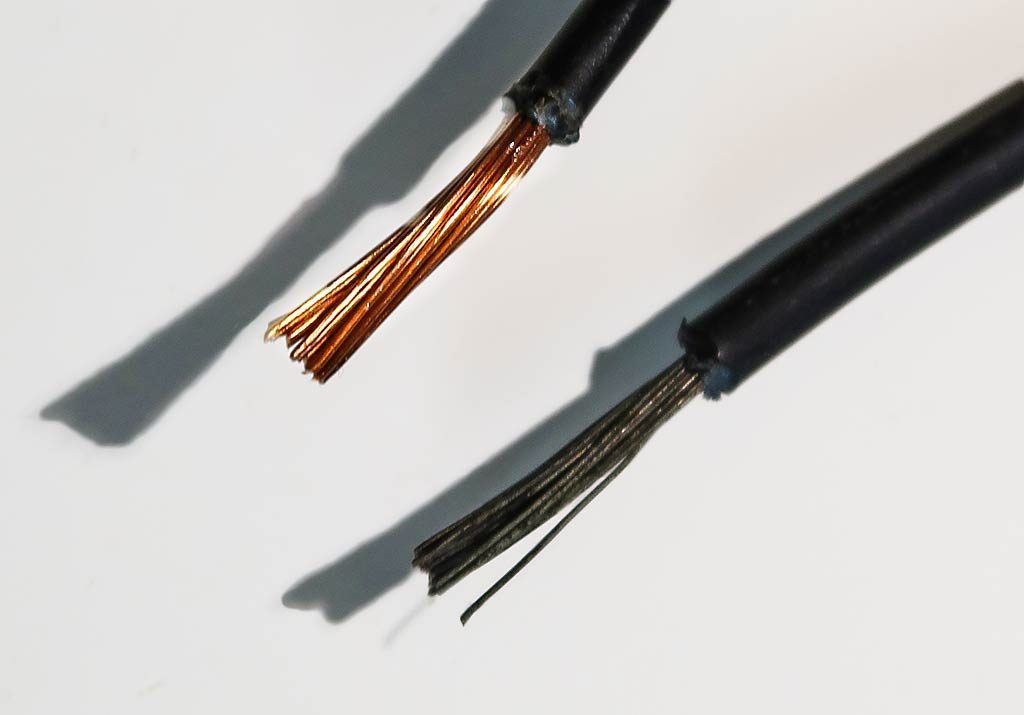
With all the rewiring I’ve done on Legacy, it’s amazing, but there is still some of the original wire from when Legacy was built 30 years ago. Some of that wire isn’t tinned, like the top wire in the picture above. I’m always amazed when I strip a wire to find shiny, perfect copper under the insulation. How can that be?
How can it be, especially when some of my recently installed, tinned wire looks so bad. The bottom wire in the photo is no more than three years old. It’s Anchor wire (I think) and supposed to be good quality. That nasty, oxidized spot wasn’t at a connector, it was in the middle of a wire run. A run not in the bilge or anywhere else where it was exposed to salt water, but in the cabin. Both of these wires came from the same area. I find this corroded, tinned wire often.
I guess my conclusion is that quality wire is not just about the conductor, but the quality of the insulation must play an important role in its longevity. None of this oxidized wire has failed, but it concerns me.
Wire 101: A couple of things in this post didn’t make much sense to Cyndi – she’s not exactly Ms Technical – so here are some basics. All wire used in boats is (or should be) copper which corrodes easily when exposed to oxygen and moisture. Tinning adds a thin coat of, well, tin (as well as some other alloys). This helps prevent corrosion, but the tinning will also corrode, though somewhat less than bare copper. Many people believe that the best practice is to use tinned wire. Some don’t. Many European boat builders don’t use tinned wire. Tinned wire is not a part of the ABYC standards and, according to Practical Sailor, never has been.
Wire has a plastic insulating jacket that, along with electrically isolating the wire, is supposed to prevent moisture from getting at the metal core. It doesn’t always do that. Moisture can enter from the wire from the ends and travel along the wire for quite some distance. I believe that moisture can also enter through the insulation if it is not of good quality.
-Rich